El sector de los sistemas embebidos a escala mundial es un mercado enorme con una fuerte proyección de crecimiento. Se prevé que pase de 100.040 millones de dólares en 2023 a 161.860 millones en 2030, según Fortune Business Insights. Pero, como en cualquier proceso de desarrollo electrónico, tanto el desarrollo como el propio dispositivo deben ser lo más eficientes posible. Más aún cuando hablamos de sistemas embebidos diseñados para fabricarse en miles o incluso millones de unidades. En estos casos, cada hora y cada céntimo invertidos en el diseño del hardware cuentan.
Desafíos del diseño hardware
A lo largo de los años, nuestros ingenieros de hardware se han enfrentado (y resuelto) a muchos retos y problemas durante el diseño y desarrollo de hardware de sistemas embebidos y productos IoT. Retos relacionados con las especificaciones de requisitos del producto, la selección de los mejores componentes, el diseño para fabricación o las pruebas de producción.
En este artículo hemos tratado de recopilar algunos de los retos más comunes y relevantes a los que nos hemos enfrentado. Esperamos que este artículo te ayude a anticipar posibles problemas y a encontrar las mejores soluciones para tu sistema embebido.
1. PRS incompleto o mala captura de los requisitos
El primer paso en cualquier proyecto debe ser una buena definición del PRS (Product Requirement Specification, o Especificación de Requisitos del Producto). Este documento lo define el cliente y/o nuestro grupo de ingenieros. En él se describen las especificaciones relacionadas con el producto a todos los niveles: hardware, firmware, normativa, etc.
En esta fase de definición es fundamental conocer a fondo la normativa aplicable a cada producto. La normativa dependerá no solo del tipo de producto, sino también del país en el que se vaya a vender/instalar.
Algunos ejemplos de información que debería contener el PRS:
- Normas: IEC, seguridad eléctrica, etc.
- Características medioambientales: Grado de protección IP, tipo de aislamiento, rango de temperaturas.
- Características eléctricas: tensión de alimentación, rango de entrada, rango de medida (en caso de equipos de medida como contadores eléctricos), etc.
- Características mecánicas.
Una buena captación de requisitos sentará las bases para un diseño de hardware bueno y sin fisuras. Por eso siempre hay que evitar un PRS incompleto o una mala captura de requisitos.
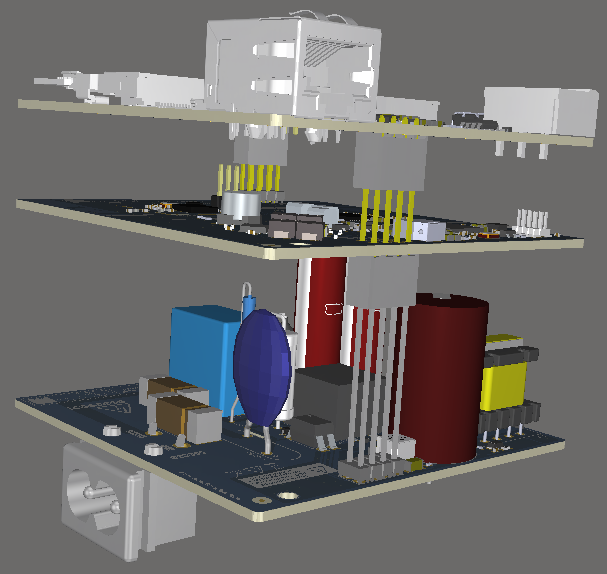
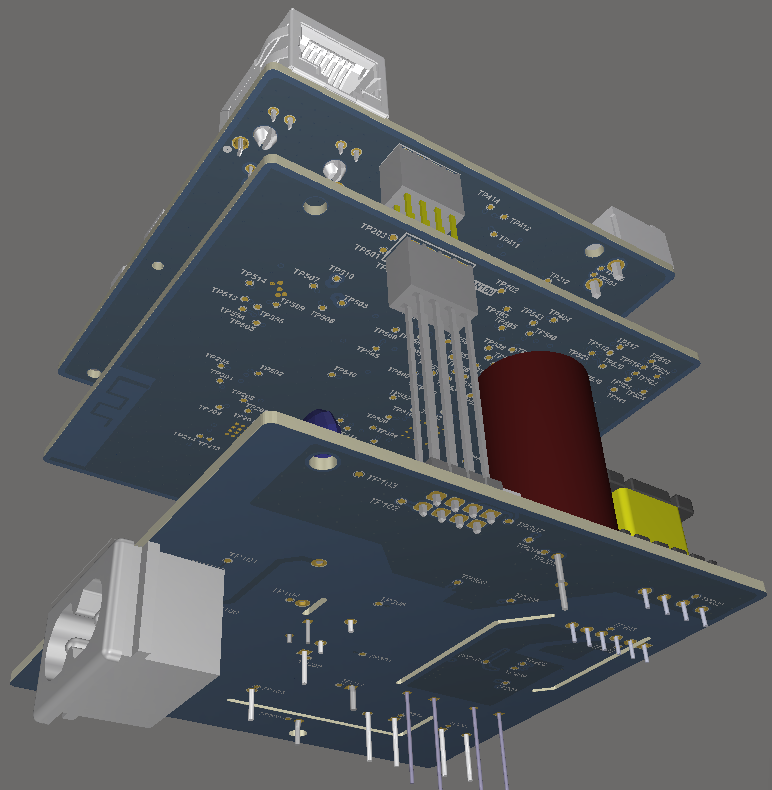

2. Encontrar el balance adecuado entre coste y calidad
El equilibrio es esencial a la hora de diseñar un producto. Una vez que se dispone de un PRS completo, el siguiente paso es la creación del HLD (High Level Design). En este documento se describen los principales bloques que formarán nuestro Hardware, así como algunos de los componentes principales para cumplir los requisitos extraídos del PRS. Esta etapa se conoce como Análisis de Requisitos.
Durante esta fase, tendrás que plantearte una serie de preguntas que te ayudarán a conseguir el equilibrio adecuado para tu producto.
¿Componentes discretos o integrados?
Normalmente, la primera opción es más barata, pero requiere más tiempo de desarrollo, por lo que es importante evaluar la previsión de producción de unidades para compensar el coste del diseño. Una solución más integrada reduce el tiempo de diseño, pero aumenta el coste final del material.
Otro punto a tener en cuenta es el espacio que ocupan los componentes. El uso de componentes discretos en ocasiones aumenta el área ocupada, mientras que el uso de componentes integrados puede llevar a una optimización del espacio utilizado, que a veces es crucial dependiendo del tipo de diseño del hardware y del espacio físico disponible para el desarrollo de la electrónica.
¿Cómo equilibrar el control de costes con la calidad y la seguridad?
La calidad y seguridad de un producto no debería ser negociable. Pero a mayor calidad y seguridad, mayores costes. Entonces, ¿dónde está el límite? ¿Cómo equilibrar el control de costes con la calidad y la seguridad?
Para encontrar este equilibrio, es muy importante definir correctamente aspectos como la tensión o corriente máximas de los componentes, la anchura o impedancia de las vías, o la holgura o fuga mínimas para cumplir los parámetros de calidad o seguridad, pero también es importante fijarlos correctamente para ahorrar costes de diseño y producción.
¿Quién fabricará mi producto?
Existen distintos fabricantes, y la calidad de servicio depende del seleccionado. Aspectos como el plazo de entrega o el volumen de producción semanal pueden ser más o menos importantes en el proyecto y hay que tenerlos en cuenta.
3. Tener un plan B a la hora de seleccionar los componentes
A la hora de seleccionar los componentes para un producto, se deben evaluar ciertos aspectos. Por ejemplo: disponibilidad de existencias o plazo de entrega en fábrica. Es importante tener claro el tiempo que se tardará en disponer de los componentes para el montaje. Un plazo de entrega elevado puede provocar retrasos en la fabricación si no se ha tenido en cuenta al realizar los pedidos de compra.
Disponer de alternativas de cada componente puede ser un salvavidas en caso de que se agoten las existencias o se produzcan subidas de precio inesperadas. Además, tener fabricantes alternativos nos dará ventaja en las negociaciones de precios con los proveedores.
Nosotros mismos hemos vivido algunas crisis de componentes, como el atentado contra las torres gemelas, que llevó a reforzar los controles fronterizos, la pandemia de COVID, con el cierre de muchas fábricas relacionadas con componentes electrónicos, o la guerra de Ucrania, con un mercado limitado y un aumento de los costes.
Tras estas experiencias, hemos aprendido que un diseño de hardware con componentes lo más básicos posible, sin exclusividad y con fácil sustitución por parte de otros fabricantes, es un enfoque bastante inteligente. El objetivo es evitar, en la medida de lo posible, el impacto de crisis externas en nuestro producto.
4. Cumplir los objetivos de eficiencia energética
En cualquier diseño de hardware, el consumo eficiente de energía debería ser siempre un aspecto relevante. Pero aún más cuando el sistema funciona con baterías. En este caso, reducir el consumo durante el funcionamiento normal o durante los momentos de inactividad debería ser uno de los principales objetivos. Esta cuestión debe abordarse desde el principio seleccionando los componentes más adecuados y creando una arquitectura de diseño de hardware correcta.
En este sentido existen estrategias para optimizar el consumo de energía teniendo en cuenta diferentes parámetros de los componentes como:
- Corriente de fuga
- Corriente de reposo de la fuente de alimentación del IC
- Corriente inversa de la fuente de alimentación del IC
Por ejemplo, si tenemos un periférico conectado a nuestro microcontrolador, debemos preguntarnos si necesita estar siempre alimentado, o si debemos añadir un interruptor de encendido para cortar la alimentación. Una buena práctica en este sentido debería ser configurar todos los pines que se conectan a ese periférico para que estén en el estado que resulte de menor consumo cuando el periférico esté sin alimentación. Mantener un pin de salida del microcontrolador a nivel alto conectado a un periférico que está apagado puede provocar un elevado consumo de fuga, por lo que es mejor configurarlo como entrada o salida a nivel bajo.
5. Orientar el diseño para la fabricación (DFM) con el objetivo de ahorrar costes
Otro de los puntos más importantes a la hora de iniciar un diseño de hardware es tener claro si estamos diseñando un prototipo de pequeños lotes o un producto que va a ensamblarse en serie de forma automatizada. En el segundo caso, el DFM es fundamental a la hora de colocar los componentes y la disposición en general.
Hay varias consideraciones a tener en cuenta para minimizar los costes de montaje y evitar sobrecostes. Por ejemplo:
- Mantener todos los componentes en un lado para reducir los costes de ensamblaje.
- Evitar los componentes con orificios, ya que suelen requerir un montaje manual o una plantilla para el montaje por ola de estaño, lo que aumenta los costes de montaje.
- Si no podemos evitar el uso de componentes TH, mantén unas distancias mínimas entre los pads de dichos componentes y los elementos circundantes para facilitar la soldadura por ola. Es habitual necesitar un mínimo de 2 mm.
- Mantener una distancia mínima entre cualquier componente y el borde de la placa para evitar daños durante el montaje de la PCB (Printed Circuit Board). Es habitual necesitar un mínimo de 3 mm.
- Y muchos más...
Además, es muy importante compartir el diseño en una fase temprana con la fábrica para realizar un análisis DFM, detectar posibles complicaciones en el futuro montaje y tomar medidas correctivas antes de finalizar el diseño.
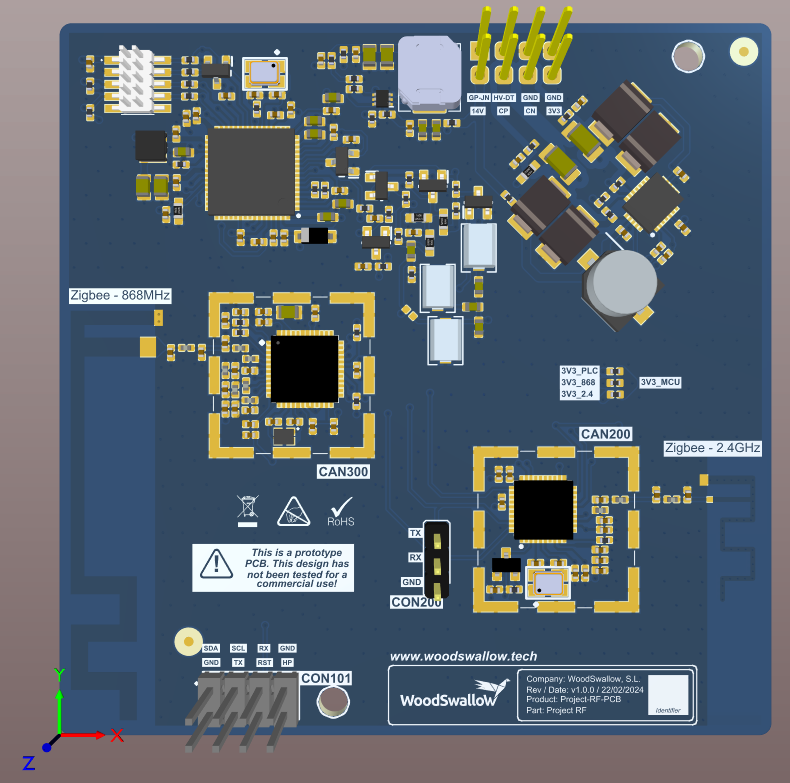
6. Dotar a la fábrica de las herramientas adecuadas para las pruebas de producción
Es crucial definir un número adecuado de puntos de prueba tanto para la fabricación como para el montaje, de modo que la placa pueda probarse durante ambos procesos. Añadir pruebas automatizadas de cada equipo una vez montado evita que cualquier fallo durante el proceso de fabricación pueda dar lugar a un producto defectuoso.
La automatización de las pruebas de los equipos en la fábrica es esencial para garantizar la fiabilidad y el ahorro de costes en el proceso de fabricación. Un paso previo es el DVT (Design Test Verification) cuando el diseño está en fase de prototipo.
En esta fase, el equipo debe probarse del mismo modo que se probará en la fábrica en el proceso de fabricación. A continuación, es muy importante ponerse en contacto con la fábrica para definir los requisitos de los puntos de prueba para la fabricación.
7. Encontrar un equipo cualificado de ingenieros de hardware
En la mayoría de los casos, el hardware de los sistemas embebidos tiene cada vez más requisitos de espacio y complejidad funcional, teniendo en cuenta multitud de factores. Por eso es necesario contar con un equipo experimentado y cualificado de ingenieros de hardware.
Es esencial que el equipo de diseño de hardware controle factores de diseño actuales como los siguientes:
- Requisitos mecánicos de las zonas restringidas, forma de la placa, interfaces, conectores, portapilas, botones, pantalla o interruptores antisabotaje.
- Bloque de fuente de alimentación con grandes holguras, trazas de gran anchura, componentes con grandes orificios pasantes, holguras en la placa hasta la línea de fuga.
- Bloque RF, SDRAM o pistas de pares diferenciales con trazas de control de impedancia, holgura específica, muchas vías para reducir las interferencias.
- Número de capas. Es aconsejable evitar las interferencias tendiendo las redes en las capas interiores y tener las mínimas distancias de pista posibles en las capas exteriores, excepto para las distancias cortas entre componentes SMD o la pequeña distancia para conectar un punto de prueba.
Y con esto concluye nuestro artículo sobre los retos más comunes durante el diseño y desarrollo de hardware para sistemas embebidos. Esperamos que te haya sido útil.
Si buscas un partner con experiencia en hardware y firmware de sistemas embebidos, ponte en contacto con nosotros y estaremos encantados de estudiar las mejores soluciones para tu producto.